Discover the Cost of Injection Moulding Dies: A Comprehensive Guide
By:Admin
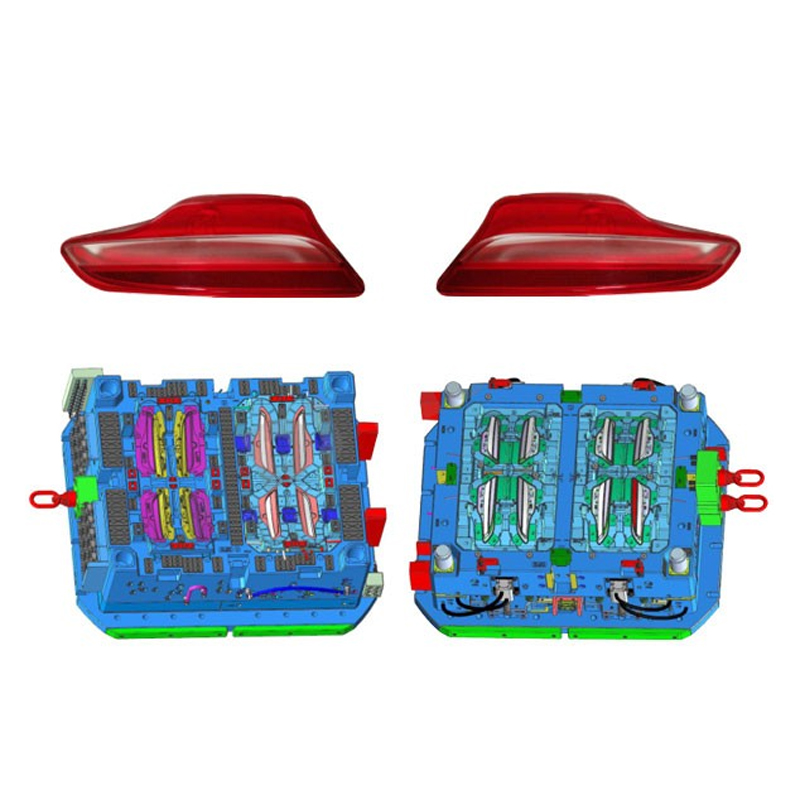
Manufacturing companies all over the world use injection moulding as one of their primary manufacturing techniques. Whether it is automotive, medical, or consumer goods, injection moulding is widely used due to its high efficiency and precision. Injection moulding die is a key component of any injection moulding operation. It is the device that shapes plastic pellets or granules into a finished product.
However, the cost of injection moulding dies can vary depending on several factors such as design, size, complexity, material, and finishing. In this article, we will discuss the various factors that impact injection moulding die costs.
Factors that Impact Injection Moulding Die Costs
Design
The design of the injection moulding die is one of the primary factors that impacts the cost. A complicated and intricate design would require more engineering time, ultimately increasing the overall cost. On the other hand, a simple design would require less engineering time and would be more cost-effective.
Size
The size of the injection moulding die plays a significant role in determining its cost. Larger dies would require more material and energy during production, increasing the overall cost. The complexity of the design would also increase with the size of the die, ultimately impacting the final cost.
Complexity
The complexity of the injection moulding die determines the amount of detail required in the design and manufacturing process. A more intricate design requires more sophisticated manufacturing techniques, ultimately resulting in a higher cost.
Material
The material used to manufacture the injection moulding die also impacts the final cost. Aluminium is a popular choice for injection moulding dies as it is cheaper, faster, and easier to manufacture. However, it is not as durable as steel and requires frequent replacement. Steel is a more expensive option, but it is more durable and can typically withstand higher temperature and pressure.
Finishing
The finishing of the injection moulding die is also a factor that affects the cost. Depending on the desired finish, additional processes such as polishing or texturing may be required, ultimately increasing the overall cost.
How to Reduce Injection Moulding Die Costs
1. Simplify the Design
As previously mentioned, the design of the injection moulding die plays a significant role in determining its cost. Simplifying the design can reduce the complexity of the manufacturing process and ultimately reduce the cost.
2. Use the Right Material
Choosing the right material for the injection moulding die can have a significant impact on the cost. Using aluminium instead of steel may be a better choice for simple products that require short production runs. On the other hand, using steel may be a better option for more complex products that require a higher degree of durability.
3. Consider the Lifecycle of the Die
Consider the lifecycle of the injection moulding die when making decisions about its production. The cost of the die is not just the upfront cost but also the cost of maintenance, repair, and replacement over its lifetime. A more expensive steel die may have a longer lifespan and require less frequent replacement, ultimately making it the more cost-effective option in the long run.
Conclusion
Injection moulding is a widely-used manufacturing technique that allows for high efficiency and precision. The cost of the injection moulding die can vary depending on several factors such as design, size, complexity, material, and finishing. However, by simplifying the design, using the right material, and considering the lifecycle of the die, manufacturers can reduce the overall cost and increase profitability. Ultimately, it is important to consider the cost-benefit analysis of the injection moulding die to ensure that the final product meets the required specifications at a cost-effective price.
Company News & Blog
Top Supplier of Gas Injection Moulding in China" could be rewritten as "Leading Gas Injection Moulding Supplier in China
China-based Gas Injection Moulding Supplier, one of the leading providers of gas injection moulding technology, has recently made significant strides in the global market. With its innovative solutions and a broad range of offerings, China Gas Injection Moulding Supplier has positioned itself as a reliable and capable partner for businesses seeking cost-effective and efficient moulding solutions.Gas injection moulding is a process that involves injecting gas into a mould cavity to create hollow parts with intricate designs. This technology offers several advantages over traditional moulding methods, including reduced material usage and cycle time, improved part quality and consistency, and increased design flexibility. It is widely used in various industries, such as automotive, consumer goods, electronics, and medical devices.China Gas Injection Moulding Supplier stands out in the market due to its cutting-edge technology, extensive industry experience, and dedication to customer satisfaction. The company's team of experts works closely with clients to understand their specific requirements and provide tailored solutions that meet their production needs.One of the key factors behind China Gas Injection Moulding Supplier's success is its commitment to continuous innovation. The company invests heavily in research and development to stay at the forefront of the gas injection moulding technology. By continuously improving their manufacturing processes and adopting new technologies, China Gas Injection Moulding Supplier ensures that its customers benefit from the latest advancements in the industry.Furthermore, China Gas Injection Moulding Supplier has established a strong quality management system to ensure the highest standards in its products and services. The company strictly adheres to international quality standards and has obtained various certifications, including ISO 9001. With a dedicated quality control team, China Gas Injection Moulding Supplier conducts rigorous testing and inspection at every stage of the manufacturing process to guarantee the reliability and durability of its products.In addition to its technological advancements and focus on quality, China Gas Injection Moulding Supplier boasts a robust global supply chain network. The company has built long-term partnerships with reliable raw material suppliers, ensuring a stable and uninterrupted supply of high-quality materials. This, combined with its efficient production processes and skilled workforce, enables China Gas Injection Moulding Supplier to deliver products promptly and maintain a competitive edge in the market.China Gas Injection Moulding Supplier's dedication to customer satisfaction is evident in its outstanding after-sales service. The company offers comprehensive support, including technical assistance, troubleshooting, and maintenance services, to ensure that its customers experience a smooth and problem-free production process.As a market leader, China Gas Injection Moulding Supplier is committed to sustainable and responsible manufacturing practices. The company prioritizes environmental protection and resource conservation in its operations. By leveraging innovative technologies and optimizing production processes, China Gas Injection Moulding Supplier minimizes waste generation and energy consumption, contributing to a greener planet.In conclusion, China Gas Injection Moulding Supplier has emerged as a prominent player in the global gas injection moulding market. With its advanced technology, focus on quality, efficient supply chain, and customer-oriented approach, the company continues to gain recognition and trust from customers worldwide. As the demand for gas injection moulding solutions continues to grow, China Gas Injection Moulding Supplier is well-positioned to meet the needs of businesses across various industries.
How to Clean and Prevent Household Mold in Your Home
Household Mold Line Expands Its Services to Help Homeowners Prevent and Remove MoldAs the weather continues to shift from one extreme to the other, homeowners across the country are facing a growing problem: mold. Mold can cause a wide range of health problems, from allergies and asthma to respiratory infections and even cancer. And, because mold loves to grow in damp, humid areas, it can be very hard to prevent or get rid of it entirely.Fortunately, there is now a solution: Household Mold Line, a leading provider of mold prevention and removal services. Founded in 2012, the company has quickly become known for its effective, affordable solutions to household mold problems. And, with the recent expansion of its services, it is poised to become one of the most sought-after mold remediation companies in the industry.At its core, Household Mold Line is a family-owned and operated business that truly understands the importance of keeping homes safe and healthy. Unlike other mold remediation companies, which may use harsh chemicals or techniques that can damage your home, Household Mold Line uses only safe, environmentally-friendly products and tools to get rid of mold. This means that, not only will your home be free from mold, but you won’t have to worry about any harmful chemicals lingering behind.The company’s comprehensive services start with a thorough inspection of your home to identify any areas where mold may be hiding. From there, the team at Household Mold Line will work with you to create a customized plan to eliminate the mold and prevent it from coming back. Whether you need help with mold in your basement, bathroom, or elsewhere in your home, Household Mold Line has the expertise, tools, and resources to get the job done right.But that’s not all. In addition to its mold removal services, Household Mold Line also offers a range of preventative solutions to help keep your home mold-free. These include:- Humidity control: Humid environments are breeding grounds for mold, so Household Mold Line can install humidity control systems that will keep the air in your home dry and comfortable.- Insulation: Proper insulation can help prevent mold by reducing condensation and keeping your home’s temperature consistent. Household Mold Line can install new insulation or replace old, ineffective insulation to improve your home’s resistance to mold.- Waterproofing: If your home is prone to flooding or water damage, waterproofing can be a great way to protect your property from future mold growth. Household Mold Line can install waterproof barriers in your basement or crawlspace to prevent water intrusion and keep mold at bay.With these preventative solutions, you can rest assured that your home will be protected from mold growth for years to come.So, what sets Household Mold Line apart from other mold remediation companies? In addition to its commitment to eco-friendly solutions and high-quality workmanship, Household Mold Line is also dedicated to providing top-notch customer service. The company’s team of certified technicians will go above and beyond to ensure that you are completely satisfied with the results of their work. And, if you ever have any questions or concerns, they are always available to provide guidance and support.Overall, Household Mold Line is a company that truly cares about its customers and their well-being. Whether you are dealing with a current mold problem or simply want to prevent one from occurring, Household Mold Line has the solutions you need to keep your home healthy and safe. To learn more about the company’s services or to schedule a consultation, visit their website today.
Understanding the Factors Affecting Injection Molding Mold Costs
Title: The Significance of Cost-Efficient Injection Molding Molds in Manufacturing IndustryIntroduction:In today's competitive manufacturing landscape, companies are constantly seeking cost-effective solutions to maintain their competitiveness and drive profitability. One such solution is the utilization of injection molding molds, which significantly reduces production costs and enhances overall efficiency. This article will explore the importance of cost-efficient injection molding molds and how they have revolutionized the manufacturing industry.The Dynamism of Injection Molding:Injection molding is a widely used manufacturing process that involves the creation of three-dimensional objects by injecting molten material into a mold cavity. This technique has gained popularity due to its ability to achieve high precision, efficiency, and repeatability in producing intricate parts and components for various industries.The critical role of Injection Molding Molds:Injection molding molds form the foundation of the entire injection molding process. These molds are precision-engineered structures that determine the final shape and quality of the manufactured product. Investing in high-quality, cost-efficient molds is crucial for companies aiming to achieve consistent product quality, reduce cycle time, and optimize production costs.The Cost Factor:Manufacturers are continually striving to reduce costs without compromising on the quality of their end products. Injection molding molds play a vital role in this pursuit, as they significantly impact the production costs. The initial purchase cost of the mold, although a considerable investment, is usually offset by the long-term advantages it offers, such as high productivity, low maintenance, and extended mold lifespan.Factors Influencing Injection Molding Mold Cost:Several factors determine the cost of injection molding molds, including the complexity of the design, size, material selection, and expected product output. Skilled mold designers and engineers analyze these factors to create molds that are not only cost-effective but also guarantee high-quality end products.The Role of Proper Mold Design:A well-designed injection molding mold is critical for efficient production runs. It minimizes material waste, reduces cycle times, and optimizes the overall production process. Skillful mold designers ensure that the mold design maximizes the use of available space, minimizes the number of moving parts, and incorporates cooling channels effectively, thus making the entire process more cost-efficient.Investing in Durable Materials:The choice of mold material also significantly influences mold cost and performance. Durable and high-quality mold materials, such as steel alloys, offer better longevity, require less maintenance, and exhibit superior resistance to wear and tear during production runs. Although initially more expensive, these materials result in cost savings in the long run by reducing production downtime and minimizing the need for mold replacements or repairs.The Impact of Advanced Technology:Technological advancements have further enhanced the cost-effectiveness of injection molding molds. Computer-aided design (CAD) and computer-aided manufacturing (CAM) software have revolutionized the mold design process, streamlining production and reducing time and cost involved. In addition, the use of advanced machining techniques, such as CNC (Computer Numeric Control), allows for improved precision and accuracy, resulting in high-quality molds that are built to last.The Scope for Collaboration:Collaboration between manufacturers and mold suppliers is advantageous for both parties. A close working relationship enables manufacturers to convey their specific requirements, global design standards, revision needs, and cost constraints to mold suppliers. By understanding their customer's demands, mold suppliers can offer suitable design suggestions and innovative ideas that optimize the overall mold production process and reduce costs.Conclusion:Injection molding molds play a pivotal role in the manufacturing industry by enabling cost-effective production and maintaining product quality. Through proper mold design, the selection of durable materials, and the utilization of advanced technologies, companies harness the benefits of efficient mold production, reducing costs, and increasing profitability. The continual innovation and collaboration between manufacturers and mold suppliers are vital for staying ahead in the competitive global market.
How Recycled Plastic Moulding is Revolutionizing Manufacturing
Recycling plastic is one of the most efficient ways to promote environmental sustainability. In recent years, the demand for recycled plastic products has been increasing, and manufacturers are responding by investing in innovative recycling solutions. One such company that has been leading the way in recycled plastic moulding is {brand name removed}.{Brand name removed} is a global leader in the production of recycled plastic moulding products. The company was founded in the early 1970s and has since been committed to developing and producing innovative recycling solutions that meet the needs of its clients. With a strong focus on research and development, {brand name removed} has been able to produce a range of high-quality products that are not only eco-friendly but also cost-effective.{Brand name removed}'s plastic moulding processes are designed to create products with unparalleled precision and accuracy. The company uses a range of state-of-the-art equipment and machinery to create complex and intricate designs. Moreover, they are able to produce customised recycled plastic products that perfectly match their clients' requirements.One of the key advantages of using {brand name removed}'s recycled plastic moulding products is their durability. Recycled plastic products from {brand name removed} are resistant to corrosion, weathering and wear and tear. As a result, they are ideal for use in a range of applications, including construction, automotive, and telecommunications.{Brand name removed} has a comprehensive range of recycled plastic moulding products that cater to their clients' diverse needs. The company's product portfolio includes cable management systems, safety barriers, bollards, custom components, and fuel tanks. All their products are made from 100% recycled plastic materials, making them eco-friendly and sustainable.{Brand name removed} is committed to providing the highest quality services to its clients. The company's philosophy is centered on meeting and exceeding customer expectations, and they go the extra mile to ensure their clients are satisfied with their products and services. They work closely with their clients to understand their requirements and propose innovative solutions that meet their needs.The company's manufacturing processes are certified to international standards, including ISO 9001, which affirms their commitment to quality. Their team of experienced professionals are highly skilled in the art of recycled plastic moulding, and they use their expertise to develop solutions that enable their clients to achieve their desired outcomes.Despite their extensive range of high-quality recycled plastic products, {brand name removed} remains committed to continuous improvement and innovation. They invest heavily in research and development as part of their commitment to reducing the environmental impact of their products. The company is constantly exploring new and innovative recycling solutions that can make their products even more eco-friendly and sustainable.In conclusion, {brand name removed} is a global leader in the production of recycled plastic moulding products that are durable, efficient, cost-effective, and environmentally friendly. The company's products are ideal for use in a wide range of applications, thanks to their superior performance and resistance to wear and tear. With a commitment to quality service, innovative solutions, and continuous improvement, {brand name removed} is poised to remain at the forefront of recycled plastic moulding for years to come.
Discover the Latest Advancements in Jumbo Bin Mould Production
[Title]Leading Manufacturer Introduces Advanced Jumbo Bin Mould, Revolutionizing Warehouse Storage Solutions[Introduction]In an era where efficiency and sustainability are paramount, the manufacturing industry continuously seeks innovative solutions that can optimize processes while minimizing costs. Addressing this need, a prominent manufacturer has recently announced the development of a cutting-edge Jumbo Bin Mould, poised to revolutionize warehouse storage solutions worldwide. This ground-breaking product promises to enhance storage capacity, streamline logistics operations, and contribute to a more sustainable future through its advanced design and unparalleled durability.[Company Introduction]With over two decades of experience in the manufacturing sector, our company has firmly established itself as an industry leader in the development and production of high-quality moulds. Committed to driving innovation and meeting the evolving needs of our customers, we have consistently delivered solutions that enable businesses to enhance productivity and improve their bottom line. Our dedicated team of engineers, technicians, and designers work tirelessly to deliver groundbreaking products that exceed customer expectations.[Product Overview]The recently introduced Jumbo Bin Mould represents a significant breakthrough in the field of warehouse storage solutions. This mold is designed to create large storage bins, which are used extensively across industries such as logistics, manufacturing, and retail to store and transport various materials. The innovative design, coupled with superior material selection, ensures these jumbo bins offer exceptional strength, durability, and longevity.[Benefits]The Jumbo Bin Mould offers numerous benefits that significantly improve warehouse storage efficiency. Firstly, it enables businesses to maximize their storage capacity by efficiently utilizing available space. With their large dimensions, these bins have a higher storage capacity compared to conventional storage solutions. This translates into optimized use of warehouse space, allowing organizations to store more goods in the same area.Furthermore, these jumbo bins are constructed to be stackable, facilitating efficient transportation and easy retrieval of goods. The strategic placement of reinforced handles and sturdy castors allows for seamless mobility, increasing productivity and reducing potential hazards. By improving the accessibility and maneuverability of stored materials, organizations can reduce handling time and enhance overall operational efficiency.Additionally, the Jumbo Bin Mould offers exceptional durability and resistance to impact, chemicals, and extreme temperatures. This ensures that the bins can withstand rigorous handling and harsh working environments without compromising their structural integrity. With their extended lifespan, these jumbo bins significantly reduce the need for frequent replacements, positively impacting both cost-effectiveness and environmental sustainability.[Environmental Impact]Sustainability has become a crucial aspect of modern manufacturing practices. In line with this commitment, our Jumbo Bin Mould utilizes eco-friendly materials that are free from harmful substances. By reducing waste and promoting recyclability, these bins promote green initiatives and contribute to a greener future. Furthermore, their extended lifespan and durability further minimize the carbon footprint associated with the production and disposal of alternative storage solutions.[Conclusion]As the demand for efficient and sustainable warehouse storage solutions continues to rise, our company's introduction of the groundbreaking Jumbo Bin Mould is set to reshape the industry. This innovative product, with its advanced design, increased storage capacity, and exceptional durability, offers organizations an unprecedented opportunity to optimize their logistics operations and streamline their supply chains. With the Jumbo Bin Mould, businesses can enhance productivity, reduce costs, and contribute towards a more sustainable future.
Discover the Latest Innovation in Cavity Pet Blowing Machines
Introducing the New and Efficient 2 Cavity Pet Blowing Machine for Enhanced Manufacturing ProcessesThe manufacturing industry is constantly evolving, with machines becoming more advanced to meet the growing demands of the market. In line with this, we are excited to introduce our latest innovation, the 2 Cavity Pet Blowing Machine, designed to revolutionize the production of PET bottles.This cutting-edge machine is unlike any other, boasting a formidable range of features that make it a game-changer within the industry. Its efficient design allows for the simultaneous production of two PET bottles, significantly increasing output and saving valuable time during the manufacturing process. With this machine, manufacturers can effectively double their production capacity, leading to improved profitability and customer satisfaction.One of the main benefits of our 2 Cavity Pet Blowing Machine is its ability to produce bottles of varying sizes and shapes without compromising on quality. Its versatility means that manufacturers can cater to the diverse needs and preferences of consumers, expanding their product offerings and staying ahead of their competitors. Whether it's small or large bottles, round or square containers, this machine can handle it all with ease.In addition to its versatility, our 2 Cavity Pet Blowing Machine is also renowned for its efficiency and precision. Equipped with advanced technology, it ensures that each bottle is perfectly shaped and durable. The machine's automated design streamlines the production process, reducing the need for manual labor and minimizing human error. This not only saves time but also cuts down on production costs, ultimately increasing the overall profitability of manufacturing operations.Furthermore, we have placed great emphasis on the sustainability aspect of our 2 Cavity Pet Blowing Machine. With increasing global concerns over environmental issues, manufacturers are seeking solutions that align with their green objectives. Our machine is designed to reduce energy consumption, resulting in lower carbon emissions and a reduced environmental footprint. By investing in this machine, manufacturers can demonstrate their commitment to sustainable manufacturing practices and gain a competitive edge in the market.To ensure our customers receive the full benefits of our 2 Cavity Pet Blowing Machine, we offer comprehensive after-sales support and maintenance services. Our team of highly skilled technicians is available to provide training and assistance, ensuring smooth and trouble-free operations. Additionally, our customer service representatives are always ready to answer inquiries and address any concerns that may arise.As a leading player in the manufacturing industry, we are committed to delivering exceptional quality and innovative solutions. Our 2 Cavity Pet Blowing Machine is a testament to our dedication to meeting the evolving needs of our customers. With its advanced features, efficiency, precision, and sustainability, this machine is set to revolutionize the PET bottle manufacturing process.In conclusion, the introduction of our 2 Cavity Pet Blowing Machine brings a new level of efficiency, versatility, and sustainability to the manufacturing industry. With its ability to simultaneously produce two high-quality PET bottles of varying sizes and shapes, this machine represents a significant advancement for manufacturers. Emphasizing precision and energy efficiency, it sets a new industry standard. By investing in our 2 Cavity Pet Blowing Machine, manufacturers can accelerate their production capacity, reduce costs, and demonstrate their commitment to sustainable manufacturing practices. We are excited to collaborate with manufacturers in achieving their production goals and staying ahead in this ever-evolving industry.
How to Reduce Injection Molding Tooling Costs for Your Business
Injection Molding Tooling CostInjection molding is a widely used manufacturing process that enables the production of high-quality plastic parts in large volumes. It involves injecting molten plastic material into a mold cavity, allowing it to cool and solidify before ejecting the finished product. While injection molding offers numerous advantages in terms of efficiency and product quality, one crucial factor that companies need to consider is the cost of tooling.Tooling refers to the design and manufacture of the molds and associated components required for injection molding. These molds play a critical role in determining the final product's shape, size, and quality. Therefore, investing in high-quality tooling is crucial for achieving optimal results. However, tooling costs can vary significantly depending on various factors such as the complexity of the part, the material used, and the production volume.Brand X, a leading manufacturer in the injection molding industry, understands the importance of providing top-notch tooling solutions while keeping costs reasonable. With its extensive experience and cutting-edge technology, Brand X has developed a streamlined process that ensures efficient tooling production without compromising on quality.The first step in the tooling process is design and engineering. Brand X employs a team of experienced engineers who work closely with clients to develop precise and robust mold designs. Utilizing advanced CAD software, they can simulate the injection molding process, identifying potential design flaws and optimizing the mold's performance. This meticulous approach helps minimize costly mistakes and reduces the need for design revisions.Once the mold design is finalized, Brand X utilizes state-of-the-art machining equipment to manufacture the tooling components. Precision CNC milling and electrical discharge machining (EDM) techniques ensure that the molds are manufactured to the exact specifications, allowing for consistent and high-quality production runs. Brand X's commitment to using the latest technology enables faster turnaround times and reduces production costs.Furthermore, Brand X understands that different projects require different molds. Some products may require simple, single-cavity molds, while others may necessitate complex multi-cavity molds to maximize productivity. With its expertise in tooling design and production, Brand X can optimize mold designs to minimize material waste and increase production efficiency. This ultimately helps reduce tooling costs for clients.In addition to initial tooling costs, maintenance and repair expenses are essential considerations. Over time, molds may experience wear and tear, resulting in reduced product quality and increased production downtime. Brand X offers comprehensive maintenance and repair services that help prolong the lifespan of the molds, minimizing long-term costs for clients. By regularly inspecting and repairing molds, Brand X ensures that they remain in optimal condition, enabling consistent production runs and reducing the need for costly mold replacements.Another cost-saving factor provided by Brand X is its ability to accommodate varying production volumes. Whether a client requires low-volume prototyping or high-volume mass production, Brand X can adapt its tooling solutions to meet their needs. This scalability allows companies to optimize their production processes without incurring unnecessary tooling expenses.In conclusion, injection molding tooling cost is a significant consideration for any company looking to utilize this manufacturing process. Brand X's commitment to providing high-quality tooling solutions at reasonable costs sets it apart in the industry. From meticulous mold design and advanced machining techniques to comprehensive maintenance services, Brand X ensures efficient production runs while minimizing expenses. By partnering with Brand X, companies can benefit from cost-effective tooling solutions without compromising on product quality or production efficiency.
Affordable Vegetable Crate Mould Manufacturer Sheds Light on the Industry
In the world of manufacturing, technology and innovation go hand in hand with quality and safety. And for companies that specialize in creating molds for plastic products, this is especially true. One such company that has made a name for itself as a premier manufacturer of high-quality molds is Cheap Vegetable Crate Mould Manufacturer.Based in China, Cheap Vegetable Crate Mould Manufacturer has been in the business of producing molds since 1998. Over the years, the company has grown in size and reputation, thanks to its commitment to excellence in everything it does. With a team of experienced and highly skilled professionals, Cheap Vegetable Crate Mould Manufacturer is dedicated to providing its clients with the best possible solutions for their needs.One of the areas in which Cheap Vegetable Crate Mould Manufacturer excels is in the creation of molds for vegetable crates. These crates are an essential tool in the agriculture industry, used for transporting and storing produce. As such, they need to be durable, reliable, and able to withstand the rigors of everyday use. And this is where Cheap Vegetable Crate Mould Manufacturer comes in.With years of experience in the field, Cheap Vegetable Crate Mould Manufacturer has developed a deep understanding of what it takes to create molds that meet the needs of the agriculture industry. From design to production, the company is committed to delivering high-quality molds that are not only effective but also cost-effective for its customers.In addition to its focus on vegetable crate molds, Cheap Vegetable Crate Mould Manufacturer offers a wide range of other products and services. These include molds for plastic chairs, pallets, buckets, and more. The company also provides customization services, allowing clients to create molds that meet their specific requirements. And with a reputation for quality and reliability, Cheap Vegetable Crate Mould Manufacturer is the go-to choice for customers around the world.But what sets Cheap Vegetable Crate Mould Manufacturer apart from its competitors? According to the company, it is its dedication to quality and innovation. The team at Cheap Vegetable Crate Mould Manufacturer is constantly looking for ways to improve its products and services, using the latest technology and techniques to stay ahead of the curve. And with a commitment to customer satisfaction, the company is always ready and willing to go the extra mile to ensure that its clients are happy with their results.For customers in need of high-quality molds for their plastic products, Cheap Vegetable Crate Mould Manufacturer is the clear choice. With years of experience, expert knowledge, and a commitment to excellence, the company offers a comprehensive range of products and services that are designed to meet the needs of a wide variety of industries. And with a reputation for quality and reliability, Cheap Vegetable Crate Mould Manufacturer is poised to continue growing and expanding into the future.
Understanding the Concept of Molding Over Molding for Enhanced Product Manufacturing
Title: Revolutionary Molding Over Molding Technology Pioneered by [Company Name]Introduction:[Company Name], a leading innovator in the manufacturing industry, has recently introduced a groundbreaking technology called Molding Over Molding (MOM). This cutting-edge technique revolutionizes the conventional manufacturing process, offering unparalleled advantages in terms of efficiency, cost-effectiveness, and product quality. MOM has already garnered widespread attention and is poised to disrupt the market, making [Company Name] a frontrunner in molding technology.Body:1. Understanding Molding Over Molding (MOM):Molding Over Molding is a sophisticated technology that involves the layering or combining of two or more materials during the molding process. The technique enables the integration of various materials such as elastomers, plastics, or metals to create highly functional and durable products. By fusing different materials together, MOM eliminates the need for multiple manufacturing steps, reducing costs and increasing overall efficiency.2. Advantages of Molding Over Molding:a) Enhanced Product Design and Functionality: MOM allows companies to design products with complex geometries, intricate patterns, and multiple functionalities. This technique facilitates customization, enabling the production of unique, innovative, and ergonomic products that meet the ever-evolving demands of consumers.b) Improved Durability and Aesthetics: By combining different materials, MOM creates products that are more resistant to wear, tear, and impact. The integration of hard and soft materials enhances the overall durability, while the smooth transition between materials results in visually appealing and seamless product finishes.c) Cost Efficiency: Molding Over Molding eliminates the need for additional assembly and bonding processes. By consolidating various manufacturing steps into a single procedure, the technology significantly reduces production costs, while maintaining superior product quality. Furthermore, MOM reduces material waste and minimizes the risk of errors or defects, further contributing to cost savings.d) Streamlined Production Process: With Molding Over Molding, companies can achieve a streamlined and simplified manufacturing process, resulting in faster production cycles and increased productivity. The reduced number of steps involved in the manufacturing process allows for shorter lead times, facilitating quick response to market demands and gaining a competitive edge.3. Application Areas of Molding Over Molding:The versatility of Molding Over Molding makes it suitable for a wide range of industries and applications, including:a) Automotive Industry: MOM can be utilized in the production of vehicle components such as interior panels, instrument clusters, steering wheels, and gear shifters. The technology enables the integration of different materials, providing enhanced comfort, safety, and aesthetics.b) Electronics: Molding Over Molding is highly relevant in the electronics industry, where it can be employed in the manufacturing process of device casings, keypads, connectors, and cables. The technique ensures robustness, waterproofing, and longevity of electronic products.c) Medical Devices: MOM can play a vital role in the production of medical devices such as surgical instruments, drug delivery systems, hearing aids, and prosthetics. The ability to combine materials with varying properties enables the creation of innovative, patient-centric, and efficient healthcare solutions.d) Consumer Goods: Manufacturers of consumer goods can utilize Molding Over Molding to develop superior-quality products such as kitchenware, toys, and sporting equipment. The technique allows for the creation of aesthetically pleasing, durable, and ergonomic items that enhance user experience.4. [Company Name]'s Leadership in Molding Over Molding:[Company Name] has been at the forefront of manufacturing innovation for over [number of years] years. The introduction of Molding Over Molding technology underscores their commitment to providing industry-leading solutions to their clients. With a team of experienced engineers and state-of-the-art facilities, [Company Name] is positioned as a pioneer in the field of MOM, aiming to reshape manufacturing processes across industries.Conclusion:The advent of Molding Over Molding technology by [Company Name] presents a paradigm shift in the manufacturing industry. This cutting-edge technique offers unprecedented advantages in design flexibility, durability, cost-efficiency, and time-saving. As companies embrace this revolutionary technology, they can enhance their product offerings, improve customer satisfaction, and gain a competitive edge in today's dynamic market landscape. With [Company Name] leading the way, Molding Over Molding technology is set to transform the way products are manufactured globally.
Twin Shot Injection Moulding: Advancements in Dual-Injection Technology
[Introduction]In recent news, an innovative and advanced manufacturing technique called Twin Shot Injection Moulding has been making waves in the industry. This groundbreaking technology offers significant advantages over traditional methods, improving efficiency, reducing costs, and enhancing product quality. In this article, we will explore the various benefits of Twin Shot Injection Moulding and showcase its potential applications across different industries.[Company Introduction]{Company Name}, a leading provider of cutting-edge manufacturing solutions, has been at the forefront of the development and implementation of Twin Shot Injection Moulding technology. With years of experience and expertise, the company has revolutionized the manufacturing process, enabling businesses to maximize their production capabilities and stay ahead of the competition.[Twin Shot Injection Moulding: The Game-Changer]Twin Shot Injection Moulding is an advanced manufacturing technique that allows the production of complex and intricate products with unparalleled precision and accuracy. The process involves injecting two different materials or colors into a single mould simultaneously, resulting in a final product with unique properties and designs. This technique offers several distinct advantages over conventional injection moulding methods.Firstly, Twin Shot Injection Moulding eliminates the need for secondary assembly processes, saving valuable time and effort. By combining two different materials in a single step, the technology streamlines the production process and enhances overall efficiency. Furthermore, this method reduces material waste as it allows for precise placement of each material, minimizing any excess or unused materials.Secondly, Twin Shot Injection Moulding enables the creation of complex designs and structures that were previously unattainable. The ability to fuse different materials or colors together opens up a myriad of possibilities for customization and product differentiation. Industries such as automotive, consumer electronics, and medical devices can benefit greatly from this technology, as it allows for the integration of multiple functionalities and aesthetics into a single component.Moreover, by utilizing Twin Shot Injection Moulding, manufacturers can achieve enhanced durability and performance in their products. The combination of materials with different physical properties creates synergistic effects, resulting in stronger and more resilient end-products. This technology also provides excellent bonding and sealing characteristics, making it ideal for applications where air or liquid tightness is required.[Twin Shot Injection Moulding: Industry Applications]The versatility and applicability of Twin Shot Injection Moulding extend across various industries. In the automotive sector, this technology can be used to create custom interior components that combine soft-touch materials with rigid inserts, providing an optimal balance of comfort and structural integrity. In consumer electronics, Twin Shot Injection Moulding allows for the integration of touch buttons, LED indicators, and ambient lighting into a single device, enhancing the user experience. The medical industry can also harness the benefits of this technology to manufacture medical devices that have specialized grips or ergonomic features, improving usability for healthcare professionals.[Conclusion]As innovation continues to shape the manufacturing landscape, Twin Shot Injection Moulding stands out as a game-changing technology that offers numerous advantages. From increased production efficiency to enhanced product quality and customization options, this technique has the potential to revolutionize various industries. As companies like {Company Name} push the boundaries of manufacturing with Twin Shot Injection Moulding, we can expect to see a new era of advanced products that are both visually captivating and functionally superior.