How to Reduce Injection Molding Tooling Costs for Your Business
By:Admin
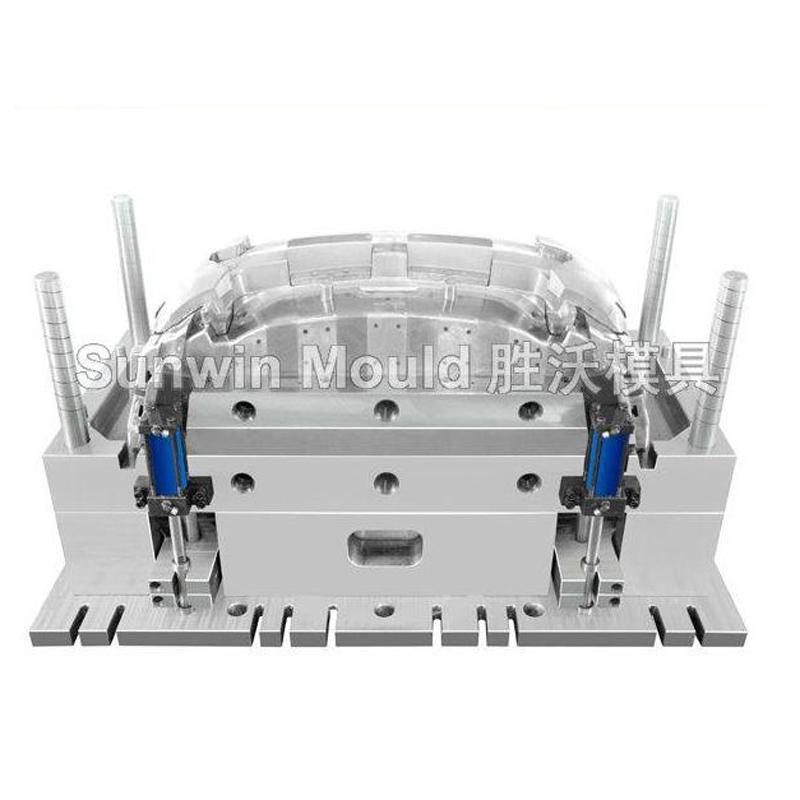
Injection molding is a widely used manufacturing process that enables the production of high-quality plastic parts in large volumes. It involves injecting molten plastic material into a mold cavity, allowing it to cool and solidify before ejecting the finished product. While injection molding offers numerous advantages in terms of efficiency and product quality, one crucial factor that companies need to consider is the cost of tooling.
Tooling refers to the design and manufacture of the molds and associated components required for injection molding. These molds play a critical role in determining the final product's shape, size, and quality. Therefore, investing in high-quality tooling is crucial for achieving optimal results. However, tooling costs can vary significantly depending on various factors such as the complexity of the part, the material used, and the production volume.
Brand X, a leading manufacturer in the injection molding industry, understands the importance of providing top-notch tooling solutions while keeping costs reasonable. With its extensive experience and cutting-edge technology, Brand X has developed a streamlined process that ensures efficient tooling production without compromising on quality.
The first step in the tooling process is design and engineering. Brand X employs a team of experienced engineers who work closely with clients to develop precise and robust mold designs. Utilizing advanced CAD software, they can simulate the injection molding process, identifying potential design flaws and optimizing the mold's performance. This meticulous approach helps minimize costly mistakes and reduces the need for design revisions.
Once the mold design is finalized, Brand X utilizes state-of-the-art machining equipment to manufacture the tooling components. Precision CNC milling and electrical discharge machining (EDM) techniques ensure that the molds are manufactured to the exact specifications, allowing for consistent and high-quality production runs. Brand X's commitment to using the latest technology enables faster turnaround times and reduces production costs.
Furthermore, Brand X understands that different projects require different molds. Some products may require simple, single-cavity molds, while others may necessitate complex multi-cavity molds to maximize productivity. With its expertise in tooling design and production, Brand X can optimize mold designs to minimize material waste and increase production efficiency. This ultimately helps reduce tooling costs for clients.
In addition to initial tooling costs, maintenance and repair expenses are essential considerations. Over time, molds may experience wear and tear, resulting in reduced product quality and increased production downtime. Brand X offers comprehensive maintenance and repair services that help prolong the lifespan of the molds, minimizing long-term costs for clients. By regularly inspecting and repairing molds, Brand X ensures that they remain in optimal condition, enabling consistent production runs and reducing the need for costly mold replacements.
Another cost-saving factor provided by Brand X is its ability to accommodate varying production volumes. Whether a client requires low-volume prototyping or high-volume mass production, Brand X can adapt its tooling solutions to meet their needs. This scalability allows companies to optimize their production processes without incurring unnecessary tooling expenses.
In conclusion, injection molding tooling cost is a significant consideration for any company looking to utilize this manufacturing process. Brand X's commitment to providing high-quality tooling solutions at reasonable costs sets it apart in the industry. From meticulous mold design and advanced machining techniques to comprehensive maintenance services, Brand X ensures efficient production runs while minimizing expenses. By partnering with Brand X, companies can benefit from cost-effective tooling solutions without compromising on product quality or production efficiency.
Company News & Blog
Twin Shot Injection Moulding: Advancements in Dual-Injection Technology
[Introduction]In recent news, an innovative and advanced manufacturing technique called Twin Shot Injection Moulding has been making waves in the industry. This groundbreaking technology offers significant advantages over traditional methods, improving efficiency, reducing costs, and enhancing product quality. In this article, we will explore the various benefits of Twin Shot Injection Moulding and showcase its potential applications across different industries.[Company Introduction]{Company Name}, a leading provider of cutting-edge manufacturing solutions, has been at the forefront of the development and implementation of Twin Shot Injection Moulding technology. With years of experience and expertise, the company has revolutionized the manufacturing process, enabling businesses to maximize their production capabilities and stay ahead of the competition.[Twin Shot Injection Moulding: The Game-Changer]Twin Shot Injection Moulding is an advanced manufacturing technique that allows the production of complex and intricate products with unparalleled precision and accuracy. The process involves injecting two different materials or colors into a single mould simultaneously, resulting in a final product with unique properties and designs. This technique offers several distinct advantages over conventional injection moulding methods.Firstly, Twin Shot Injection Moulding eliminates the need for secondary assembly processes, saving valuable time and effort. By combining two different materials in a single step, the technology streamlines the production process and enhances overall efficiency. Furthermore, this method reduces material waste as it allows for precise placement of each material, minimizing any excess or unused materials.Secondly, Twin Shot Injection Moulding enables the creation of complex designs and structures that were previously unattainable. The ability to fuse different materials or colors together opens up a myriad of possibilities for customization and product differentiation. Industries such as automotive, consumer electronics, and medical devices can benefit greatly from this technology, as it allows for the integration of multiple functionalities and aesthetics into a single component.Moreover, by utilizing Twin Shot Injection Moulding, manufacturers can achieve enhanced durability and performance in their products. The combination of materials with different physical properties creates synergistic effects, resulting in stronger and more resilient end-products. This technology also provides excellent bonding and sealing characteristics, making it ideal for applications where air or liquid tightness is required.[Twin Shot Injection Moulding: Industry Applications]The versatility and applicability of Twin Shot Injection Moulding extend across various industries. In the automotive sector, this technology can be used to create custom interior components that combine soft-touch materials with rigid inserts, providing an optimal balance of comfort and structural integrity. In consumer electronics, Twin Shot Injection Moulding allows for the integration of touch buttons, LED indicators, and ambient lighting into a single device, enhancing the user experience. The medical industry can also harness the benefits of this technology to manufacture medical devices that have specialized grips or ergonomic features, improving usability for healthcare professionals.[Conclusion]As innovation continues to shape the manufacturing landscape, Twin Shot Injection Moulding stands out as a game-changing technology that offers numerous advantages. From increased production efficiency to enhanced product quality and customization options, this technique has the potential to revolutionize various industries. As companies like {Company Name} push the boundaries of manufacturing with Twin Shot Injection Moulding, we can expect to see a new era of advanced products that are both visually captivating and functionally superior.
Enhance Production Efficiency with Tailored Graphite Molds
Custom Graphite Molds Boost Manufacturing Efficiency and PrecisionCustom graphite molds have revolutionized manufacturing industries, fuelling innovation and increasing efficiency. With high thermal conductivity, electrical conductivity, and low coefficient of thermal expansion, graphite is an excellent material for mold manufacturing. Custom graphite molds are either machined from solid blocks or fabricated by joining smaller pieces through bonding or coating.A leading supplier of custom graphite molds, located in (omitted brand name), offers a range of tailored options to suit various manufacturing needs. The company prides itself on delivering top-quality graphite products that align with customer requirements.Their skilled and experienced technicians use advanced techniques and machinery to design and manufacture highly precise and complex molds. With a commitment to quality, timeliness, and cost-effectiveness, this company has remained a leader in the graphite mold industry.Custom graphite molds are ideal for manufacturing a wide variety of products, ranging from semiconductors, electronic components, and solar cells to glass, metals, and ceramics. They are also widely used in the aerospace, medical, automotive, and defense industries.The use of custom graphite molds in such industries has resulted in increased efficiency and precision, boosting overall production output. Graphite's unique properties allow for high heat transfer, ensuring that molds remain at an optimal temperature to produce products with consistent quality.Moreover, custom graphite molds can withstand high temperatures, making them ideal for applications where other materials may fail. This property has proved especially useful in aerospace, where high-temperature and high-pressure conditions are common.Custom graphite molds also offer better surface finishes, reduce the need for complex machining, and alleviate stress on the molds and machines. Their durability reduces downtime and maintenance costs, leading to higher productivity and profitability.(omitted brand name) graphite molds come in a range of shapes, sizes, and designs, depending on the client's specifications. They can be made to produce single components or series of products. The company offers custom-designed molds for niche applications, ensuring that clients get molds tailored to their specific needs.The mold-making process comprises several stages, including prototype design, material selection, and mold creation. The company has a project team that works closely with the clients to ensure that they get the best possible molds at the most competitive rates.The team of experts uses advanced software and engineering tools to design molds that meet exact customer specifications. This process ensures that the molds are accurate and reliable, reducing waste and saving time.Furthermore, the company focuses on cost optimization, ensuring that clients get high-quality molds at the most competitive prices. They offer an excellent after-sales service, including mold repair, maintenance, and replacement.Custom graphite molds are an essential component of the manufacturing process in many industries, delivering precision and efficiency. The use of high-quality graphite molds enhances product consistency, reduces waste, and improves output. These molds provide an effective and durable solution for complex and specialized manufacturing needs.(omitted brand name) is a leading supplier of custom graphite molds, working with companies across a wide range of industries to provide bespoke solutions. Their commitment to quality, innovation, and customer satisfaction sets them apart in the graphite mold industry.
Potion Bottle Mold: Unlocking New Creative Possibilities in Crafting and Decor
Potion Bottle Mold Enhances Manufacturing Capabilities in the Magic Elixir Industry(Date), (City) - The leading provider of mold manufacturing solutions, (Company Name), now offers the innovative Potion Bottle Mold to help revolutionize the magic elixir industry. With its state-of-the-art design and commitment to quality, the Potion Bottle Mold is set to streamline production processes, uphold safety standards, and meet the growing demand for enchanting elixirs.(Company Name) is renowned for its expertise in creating molds for various industries, including packaging, automotive, and consumer goods. With their latest offering in the form of the Potion Bottle Mold, they aim to assist companies in the magic elixir industry to optimize their manufacturing capabilities and improve efficiency.The Potion Bottle Mold boasts cutting-edge features that align with the enchanting arts, making it an indispensable tool for potion manufacturers. This innovative mold facilitates the production of various potion bottle designs, catering to the diverse needs of potion makers worldwide. The mold enables manufacturers to create elegant and visually appealing bottle shapes, enhancing the overall presentation of their magic elixirs.One of the key advantages of the Potion Bottle Mold is its ability to ensure the safety and quality of the magic elixirs. The mold is designed to prevent contamination and maintain the potency of delicate potions. It provides an airtight seal, reducing the risk of oxidation and ensuring the longevity of the elixirs' enchanted properties until they reach the consumers.Furthermore, (Company Name) has incorporated advanced materials into the Potion Bottle Mold's construction to ensure durability and longevity. The mold is crafted with high-quality, food-grade materials that meet the strictest safety standards. This ensures that manufacturers can produce potions that are safe for consumption and enchantment without compromising on quality.To stay ahead and provide the best solutions to the magic elixir industry, (Company Name) has collaborated with potion manufacturers to deeply understand their requirements and challenges. This close cooperation has allowed them to develop a mold that not only meets existing needs but also prepares potion makers for future possibilities in the industry."We are thrilled to introduce the Potion Bottle Mold to the magic elixir industry," said (Spokesperson Name), (Title) at (Company Name). "Our aim is to bring efficiency and quality to the manufacturing processes of potion makers worldwide. We understand the unique challenges faced by the industry, and we have designed this mold to cater specifically to their needs."The Potion Bottle Mold has already garnered significant attention from leading potion manufacturers. They appreciate (Company Name)'s commitment to providing tailored solutions that align with their industry's specific requirements. Recognizing the importance of efficient production processes and maintaining the highest quality standards, potion manufacturers have embraced the Potion Bottle Mold as a game-changer in their operations.In addition to the Potion Bottle Mold, (Company Name) offers comprehensive support throughout the mold manufacturing process. Their team of experts assists potion manufacturers in designing customized molds, optimizing manufacturing workflows, and implementing quality control measures. This holistic approach ensures that potion makers can maximize their production capabilities while adhering to the highest standards of quality and safety.With the introduction of the Potion Bottle Mold, (Company Name) is poised to make a significant impact on the magic elixir industry. By combining their expertise in mold manufacturing with a deep understanding of the industry's needs, they are set to enhance production processes, improve potion quality, and elevate the overall experience for potion makers and enthusiasts alike.
Discover Precision Injection Molding Techniques for High-Quality Plastic Parts
Title: Advancements in Plastic Molding Propels Manufacturing Industry ForwardIntroduction:The field of plastic molding has witnessed remarkable advancements over the years, resulting in a significant transformation of the manufacturing industry. One prominent player in this sector, referred to as "Prototype Plastic Molding" in this article, has emerged as a pioneer in delivering cutting-edge plastic molding solutions. Throughout this news article, we will explore the ongoing developments in plastic molding technology and delve into the capabilities of this leading company.1. The Evolution of Plastic Molding:The integration of advanced technologies has revolutionized the plastic molding industry, enhancing its efficiency, precision, and overall productivity. Traditional molding methods have been replaced by innovative techniques, with a strong focus on automation and computer-controlled processes. As a result, manufacturers are now able to produce complex and intricate plastic components with unmatched accuracy.2. Introduction to Prototype Plastic Molding:Prototype Plastic Molding, a globally recognized company, has been at the forefront of transforming the plastic molding landscape. With a strong emphasis on research and development, the company has consistently pushed the boundaries of manufacturing capabilities. They specialize in providing high-quality plastic parts to various industries such as automotive, electronics, medical, and consumer goods.3. Advanced Technologies:Prototype Plastic Molding has successfully adopted and integrated several advanced technologies within its manufacturing processes. The company utilizes computer-aided design (CAD) software to create precise digital models of the desired plastic components. These models are then translated into instructions for computer numerical control (CNC) machines, which enable the production of molds with extreme precision. Moreover, the company incorporates state-of-the-art 3D printing technologies to create prototypes before mass production, thereby ensuring the seamless development of new products.4. Enhanced Prototyping Capabilities:Through the utilization of their advanced CAD software and 3D printing technologies, Prototype Plastic Molding has elevated its prototyping capabilities. This enables their clients to visualize and assess the functionality, aesthetics, and ergonomics of their plastic components before final production begins. By streamlining the prototyping phase, the company diminishes the time and costs associated with product development, creating a competitive advantage for their clients.5. Emphasis on Sustainability:Prototype Plastic Molding maintains a strong commitment to sustainability, actively exploring ways to minimize waste and lower their environmental impact. The company utilizes recycled materials whenever possible, while also developing innovative solutions to optimize material usage. By implementing sustainable practices and adhering to stringent quality control measures, they ensure eco-friendly production while simultaneously meeting the evolving demands of the market.6. Cutting-edge Equipment and Expertise:Prototype Plastic Molding continuously invests in cutting-edge machinery and equipment to enhance their manufacturing capabilities. With a team of experienced professionals, they oversee every step of the production process, adhering to strict quality control standards. This holistic approach guarantees the delivery of excellent results while maintaining a rapid turnaround time for their customers.Conclusion:The advancements in plastic molding technology, spearheaded by companies like Prototype Plastic Molding, are revolutionizing the manufacturing sector. With their innovative techniques, commitment to sustainability, and expertise in delivering high-quality plastic components, Prototype Plastic Molding has earned a commendable reputation in the industry. As the manufacturing industry continues to evolve, plastic molding is expected to play an increasingly significant role, shaping the future of numerous sectors.
Understanding the Factors Affecting Injection Molding Mold Costs
Title: The Significance of Cost-Efficient Injection Molding Molds in Manufacturing IndustryIntroduction:In today's competitive manufacturing landscape, companies are constantly seeking cost-effective solutions to maintain their competitiveness and drive profitability. One such solution is the utilization of injection molding molds, which significantly reduces production costs and enhances overall efficiency. This article will explore the importance of cost-efficient injection molding molds and how they have revolutionized the manufacturing industry.The Dynamism of Injection Molding:Injection molding is a widely used manufacturing process that involves the creation of three-dimensional objects by injecting molten material into a mold cavity. This technique has gained popularity due to its ability to achieve high precision, efficiency, and repeatability in producing intricate parts and components for various industries.The critical role of Injection Molding Molds:Injection molding molds form the foundation of the entire injection molding process. These molds are precision-engineered structures that determine the final shape and quality of the manufactured product. Investing in high-quality, cost-efficient molds is crucial for companies aiming to achieve consistent product quality, reduce cycle time, and optimize production costs.The Cost Factor:Manufacturers are continually striving to reduce costs without compromising on the quality of their end products. Injection molding molds play a vital role in this pursuit, as they significantly impact the production costs. The initial purchase cost of the mold, although a considerable investment, is usually offset by the long-term advantages it offers, such as high productivity, low maintenance, and extended mold lifespan.Factors Influencing Injection Molding Mold Cost:Several factors determine the cost of injection molding molds, including the complexity of the design, size, material selection, and expected product output. Skilled mold designers and engineers analyze these factors to create molds that are not only cost-effective but also guarantee high-quality end products.The Role of Proper Mold Design:A well-designed injection molding mold is critical for efficient production runs. It minimizes material waste, reduces cycle times, and optimizes the overall production process. Skillful mold designers ensure that the mold design maximizes the use of available space, minimizes the number of moving parts, and incorporates cooling channels effectively, thus making the entire process more cost-efficient.Investing in Durable Materials:The choice of mold material also significantly influences mold cost and performance. Durable and high-quality mold materials, such as steel alloys, offer better longevity, require less maintenance, and exhibit superior resistance to wear and tear during production runs. Although initially more expensive, these materials result in cost savings in the long run by reducing production downtime and minimizing the need for mold replacements or repairs.The Impact of Advanced Technology:Technological advancements have further enhanced the cost-effectiveness of injection molding molds. Computer-aided design (CAD) and computer-aided manufacturing (CAM) software have revolutionized the mold design process, streamlining production and reducing time and cost involved. In addition, the use of advanced machining techniques, such as CNC (Computer Numeric Control), allows for improved precision and accuracy, resulting in high-quality molds that are built to last.The Scope for Collaboration:Collaboration between manufacturers and mold suppliers is advantageous for both parties. A close working relationship enables manufacturers to convey their specific requirements, global design standards, revision needs, and cost constraints to mold suppliers. By understanding their customer's demands, mold suppliers can offer suitable design suggestions and innovative ideas that optimize the overall mold production process and reduce costs.Conclusion:Injection molding molds play a pivotal role in the manufacturing industry by enabling cost-effective production and maintaining product quality. Through proper mold design, the selection of durable materials, and the utilization of advanced technologies, companies harness the benefits of efficient mold production, reducing costs, and increasing profitability. The continual innovation and collaboration between manufacturers and mold suppliers are vital for staying ahead in the competitive global market.
Understanding the Concept of Molding Over Molding for Enhanced Product Manufacturing
Title: Revolutionary Molding Over Molding Technology Pioneered by [Company Name]Introduction:[Company Name], a leading innovator in the manufacturing industry, has recently introduced a groundbreaking technology called Molding Over Molding (MOM). This cutting-edge technique revolutionizes the conventional manufacturing process, offering unparalleled advantages in terms of efficiency, cost-effectiveness, and product quality. MOM has already garnered widespread attention and is poised to disrupt the market, making [Company Name] a frontrunner in molding technology.Body:1. Understanding Molding Over Molding (MOM):Molding Over Molding is a sophisticated technology that involves the layering or combining of two or more materials during the molding process. The technique enables the integration of various materials such as elastomers, plastics, or metals to create highly functional and durable products. By fusing different materials together, MOM eliminates the need for multiple manufacturing steps, reducing costs and increasing overall efficiency.2. Advantages of Molding Over Molding:a) Enhanced Product Design and Functionality: MOM allows companies to design products with complex geometries, intricate patterns, and multiple functionalities. This technique facilitates customization, enabling the production of unique, innovative, and ergonomic products that meet the ever-evolving demands of consumers.b) Improved Durability and Aesthetics: By combining different materials, MOM creates products that are more resistant to wear, tear, and impact. The integration of hard and soft materials enhances the overall durability, while the smooth transition between materials results in visually appealing and seamless product finishes.c) Cost Efficiency: Molding Over Molding eliminates the need for additional assembly and bonding processes. By consolidating various manufacturing steps into a single procedure, the technology significantly reduces production costs, while maintaining superior product quality. Furthermore, MOM reduces material waste and minimizes the risk of errors or defects, further contributing to cost savings.d) Streamlined Production Process: With Molding Over Molding, companies can achieve a streamlined and simplified manufacturing process, resulting in faster production cycles and increased productivity. The reduced number of steps involved in the manufacturing process allows for shorter lead times, facilitating quick response to market demands and gaining a competitive edge.3. Application Areas of Molding Over Molding:The versatility of Molding Over Molding makes it suitable for a wide range of industries and applications, including:a) Automotive Industry: MOM can be utilized in the production of vehicle components such as interior panels, instrument clusters, steering wheels, and gear shifters. The technology enables the integration of different materials, providing enhanced comfort, safety, and aesthetics.b) Electronics: Molding Over Molding is highly relevant in the electronics industry, where it can be employed in the manufacturing process of device casings, keypads, connectors, and cables. The technique ensures robustness, waterproofing, and longevity of electronic products.c) Medical Devices: MOM can play a vital role in the production of medical devices such as surgical instruments, drug delivery systems, hearing aids, and prosthetics. The ability to combine materials with varying properties enables the creation of innovative, patient-centric, and efficient healthcare solutions.d) Consumer Goods: Manufacturers of consumer goods can utilize Molding Over Molding to develop superior-quality products such as kitchenware, toys, and sporting equipment. The technique allows for the creation of aesthetically pleasing, durable, and ergonomic items that enhance user experience.4. [Company Name]'s Leadership in Molding Over Molding:[Company Name] has been at the forefront of manufacturing innovation for over [number of years] years. The introduction of Molding Over Molding technology underscores their commitment to providing industry-leading solutions to their clients. With a team of experienced engineers and state-of-the-art facilities, [Company Name] is positioned as a pioneer in the field of MOM, aiming to reshape manufacturing processes across industries.Conclusion:The advent of Molding Over Molding technology by [Company Name] presents a paradigm shift in the manufacturing industry. This cutting-edge technique offers unprecedented advantages in design flexibility, durability, cost-efficiency, and time-saving. As companies embrace this revolutionary technology, they can enhance their product offerings, improve customer satisfaction, and gain a competitive edge in today's dynamic market landscape. With [Company Name] leading the way, Molding Over Molding technology is set to transform the way products are manufactured globally.
How Recycled Plastic Moulding is Revolutionizing Manufacturing
Recycling plastic is one of the most efficient ways to promote environmental sustainability. In recent years, the demand for recycled plastic products has been increasing, and manufacturers are responding by investing in innovative recycling solutions. One such company that has been leading the way in recycled plastic moulding is {brand name removed}.{Brand name removed} is a global leader in the production of recycled plastic moulding products. The company was founded in the early 1970s and has since been committed to developing and producing innovative recycling solutions that meet the needs of its clients. With a strong focus on research and development, {brand name removed} has been able to produce a range of high-quality products that are not only eco-friendly but also cost-effective.{Brand name removed}'s plastic moulding processes are designed to create products with unparalleled precision and accuracy. The company uses a range of state-of-the-art equipment and machinery to create complex and intricate designs. Moreover, they are able to produce customised recycled plastic products that perfectly match their clients' requirements.One of the key advantages of using {brand name removed}'s recycled plastic moulding products is their durability. Recycled plastic products from {brand name removed} are resistant to corrosion, weathering and wear and tear. As a result, they are ideal for use in a range of applications, including construction, automotive, and telecommunications.{Brand name removed} has a comprehensive range of recycled plastic moulding products that cater to their clients' diverse needs. The company's product portfolio includes cable management systems, safety barriers, bollards, custom components, and fuel tanks. All their products are made from 100% recycled plastic materials, making them eco-friendly and sustainable.{Brand name removed} is committed to providing the highest quality services to its clients. The company's philosophy is centered on meeting and exceeding customer expectations, and they go the extra mile to ensure their clients are satisfied with their products and services. They work closely with their clients to understand their requirements and propose innovative solutions that meet their needs.The company's manufacturing processes are certified to international standards, including ISO 9001, which affirms their commitment to quality. Their team of experienced professionals are highly skilled in the art of recycled plastic moulding, and they use their expertise to develop solutions that enable their clients to achieve their desired outcomes.Despite their extensive range of high-quality recycled plastic products, {brand name removed} remains committed to continuous improvement and innovation. They invest heavily in research and development as part of their commitment to reducing the environmental impact of their products. The company is constantly exploring new and innovative recycling solutions that can make their products even more eco-friendly and sustainable.In conclusion, {brand name removed} is a global leader in the production of recycled plastic moulding products that are durable, efficient, cost-effective, and environmentally friendly. The company's products are ideal for use in a wide range of applications, thanks to their superior performance and resistance to wear and tear. With a commitment to quality service, innovative solutions, and continuous improvement, {brand name removed} is poised to remain at the forefront of recycled plastic moulding for years to come.
China Poultry Packaging Box Mold Manufacturer Offers High-Quality Products
China Poultry Boxes Mould Manufacturer Leads the Way in Innovative Food Packaging SolutionsAs the demand for safe and sustainable food packaging continues to soar around the world, China has emerged as a prominent player in the industry. Among the many manufacturers, one company stands out for its ability to deliver cutting-edge solutions and cater to the unique needs of the global market - China Poultry Boxes Mould Manufacturer (hereafter referred to as CPC).CPC has established itself as a leading figure in the sector, driven by its commitment to innovation, quality craftsmanship, and customer satisfaction. With years of experience in the industry, the company has gained a deep understanding of the evolving demands of the poultry packaging market. By leveraging its expertise, CPC has successfully developed a range of high-quality poultry boxes moulds that have gained recognition both domestically and internationally.One of the key reasons behind CPC's success is its unwavering focus on innovation. The company employs a team of experienced designers and engineers who constantly strive to improve existing mould designs and develop new ones that are tailored to meet the unique requirements of the poultry industry. This dedication to innovation allows CPC to provide its customers with packaging solutions that not only keep their products fresh but also enhance their brand image.In addition to its commitment to innovation, CPC is known for its uncompromising approach to quality craftsmanship. The company utilizes advanced manufacturing techniques and top-of-the-line materials to produce moulds that meet the highest standards of quality. Rigorous quality control measures are followed at every stage of the production process, ensuring that each mould is free from defects and capable of withstanding the demands of the poultry packaging industry.Furthermore, CPC understands the significance of sustainability in today's environmentally conscious world. The company actively works towards reducing its environmental footprint by adopting eco-friendly practices in its manufacturing processes. CPC's moulds are designed to be reusable and highly durable, reducing waste and promoting a circular economy. By investing in sustainable packaging solutions, CPC both meets market demands and contributes to a greener and more sustainable future.CPC's dedication to customer satisfaction is another factor that sets it apart from its competitors. The company understands that each customer has unique requirements and consistently strives to meet these needs. By engaging in close collaboration with its clients, CPC ensures that its moulds are customized to their specifications, guaranteeing a perfect fit for their poultry packaging needs. The company also provides exceptional customer support services, ensuring a smooth and hassle-free experience for its clients.The success of CPC's innovative and high-quality moulds has not gone unnoticed. The products have gained significant recognition in both domestic and international markets, making the company a preferred choice among poultry packaging manufacturers. CPC's moulds have been exported to various countries, which is a testament to the company's commitment to delivering world-class products that meet global standards.Looking ahead, CPC shows no signs of slowing down its quest for innovation and excellence. The company is continuously exploring new technologies and materials to develop even more advanced and sustainable food packaging solutions. By keeping abreast of industry trends and customer demands, CPC aims to remain at the forefront of the poultry packaging market and continue its mission to provide safe, efficient, and eco-friendly packaging solutions.In conclusion, China Poultry Boxes Mould Manufacturer has established itself as a leading player in the global food packaging industry. Through its unwavering commitment to innovation, quality craftsmanship, sustainability, and customer satisfaction, CPC has become the go-to choice for poultry packaging manufacturers worldwide. With a focus on continuous improvement and a dedication to meeting the evolving demands of customers, CPC is set to shape the future of the industry and contribute to a more sustainable and efficient food packaging ecosystem.
Cutting-Edge Mold Technologies Set to Revolutionize Precision Manufacturing
Precision Mold Technologies, a leading provider of mold making and engineering solutions, has announced the expansion of its services to meet the growing demand for their high-quality products. The company is committed to providing specialized services to its customers, with a focus on meeting and exceeding their expectations in terms of quality, efficiency, and cost-effectiveness. With over thirty years of experience in the industry, Precision Mold Technologies has gained a reputation for its dedication to quality and its innovative approach to mold making. The company has invested in state-of-the-art equipment and technology to ensure that it remains at the forefront of the industry and can provide the most advanced and effective solutions to its customers. The company specializes in designing and manufacturing molds for a wide range of industries, including automotive, medical, consumer products, and electronics. By using advanced software and precision equipment, the team at Precision Mold Technologies can create complex and intricate designs that meet the exact specifications of their customers. In addition to mold making, the company also provides a range of engineering solutions, including product design, prototyping, and production. Their team of experienced engineers works closely with clients to understand their requirements and provide tailored solutions that meet their specific needs. As part of their commitment to quality, Precision Mold Technologies has implemented a rigorous quality control process to ensure that every product meets the highest standards. This includes thorough testing and inspection of every mold before it is delivered to the customer. The company is also committed to sustainability and has implemented a number of measures to reduce their environmental impact. This includes using environmentally friendly materials in their molds and ensuring that their manufacturing processes are as efficient as possible. According to Precision Mold Technologies CEO, "We are excited to announce the expansion of our services to meet the growing demand for our products. Our team is dedicated to providing the highest quality solutions to our customers, and we are confident that our expanded services will further enhance our ability to meet their needs." He further added, "We are proud of our reputation as one of the leading providers of mold making and engineering solutions in the industry, and we believe that our continued investment in technology and innovation will help us maintain this position well into the future." Customers of Precision Mold Technologies have expressed their satisfaction with the company's products and services. One customer said, "Precision Mold Technologies has been our go-to provider for mold making and engineering solutions for several years. We have always been impressed with their attention to detail and their commitment to quality. We are excited to see their continued growth and expansion, and we look forward to working with them on future projects." Another customer said, "We have been working with Precision Mold Technologies for several years, and we have always been impressed with their ability to provide customized solutions that meet our specific requirements. Their team is knowledgeable and professional, and they always go above and beyond to ensure that our needs are met. We highly recommend them to anyone looking for high-quality mold making and engineering solutions." In conclusion, Precision Mold Technologies is a company that is committed to providing high-quality mold making and engineering solutions. Their dedication to quality, innovation, and sustainability has helped them become one of the leading providers in the industry. With the expansion of their services, the company is poised to continue its growth and success well into the future. Their commitment to their customers is evident in the testimonials from satisfied customers, and their investment in technology and innovation ensures that they remain at the forefront of the industry.
How to Make Your Own Potion Bottle Mold for Halloween Crafts and Decorations
A Potion Bottle Mold Invention Sparks Interest in the IndustryA new invention, a potion bottle mold, is set to revolutionize the cosmetics industry. This invention is a game-changer for the industry as the mold is capable of creating unique, intricate, and desirable glass bottles of any shape or size. With the cut-throat competition in the cosmetics industry, this innovation is considered a welcome and necessary advancement that provides a competitive edge to manufacturers.The new potion bottle mold has been developed by a leading company in the cosmetics industry, which has been producing high-quality packaging materials for the industry for several years. The company is renowned for their quality packaging materials and their ability to provide innovative and cost-effective solutions for their clients.According to the company's website, they specialize in designing and manufacturing packaging components for a wide range of industries, including cosmetics, skincare, and pharmaceuticals. Their attention to detail, professionalism, and commitment to quality have helped them establish a loyal customer base in the industry.The newly developed potion bottle mold is the latest in their line of innovative products that are aimed at improving the customer experience and driving sales growth for their clients.The mold is produced using state-of-the-art technology and is capable of creating glass bottles of any shape or size. This provides manufacturers with endless options when it comes to designing packaging that reflects their brand and resonates with consumers.The mold has a unique feature that allows for intricate designs to be created on the surface of the bottle. This means that the bottles can be embossed or engraved with designs that complement the brand's identity and helps their products to stand out on the shelves.The potion bottle mold has been met with enthusiasm in the industry, with industry experts praising the innovation for its ability to provide manufacturers with a robust and cost-effective solution to their packaging needs. This comes at a time when the industry is experiencing increased competition, making it difficult to differentiate one product from the other.Manufacturers can now leverage the mold to create unique packaging that not only sets their products apart from their competitors but also enhances the user experience. Consumers are increasingly looking for products that are aesthetically pleasing and offer value for their money. With the potion bottle mold, manufacturers can now offer products that tick all the boxes.The mold is also cost-effective, allowing manufacturers to produce quality packaging materials at an affordable price point. This is important as packaging costs can quickly add up, especially when producing large quantities of products.In conclusion, the new potion bottle mold is set to revolutionize the cosmetics industry, providing manufacturers with a robust and cost-effective solution to their packaging needs. The mold's ability to produce unique, intricate, and aesthetically pleasing packaging materials means that manufacturers can now offer products that resonate with consumers and stand out from their competitors. With the increasing demand for quality packaging materials in the industry, the potion bottle mold is a timely innovation that is set to spark further interest in the industry.